Transport system for pallets in the pharmaceutical industry
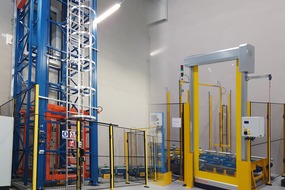
For our regular client, a Polish leader in pharmaceutical industry, we created a transportation system for plastic pallets and interlocking containers with a base typical for EUR pallets. Installation is located in new production and warehouse facility near Warsaw and is a part of complex logistics equipment supplied by PROMAG S.A.
The components of the system include: vertical transport device, buffer chain conveyors, roller transfers allowing to keep spatial orientation of pallet, static mass measurement system and contour control, high speed access gates or emergency fire gate.
The operator is dedicated to work with electric lift trucks. The operator's work area is separated from the transporting equipment by an access gate that can only be opened after the local dangerous movements have ceased. The operator confirms correct loading/unloading by means of a pull cord switch which is accessible from the platform truck. The system operates in both directions on a daily basis. The operator can book a change of direction from two unloading/loading positions.
Time, direction and weight are recorded for each transport unit. The number of pallets rejected due to outline error and exceeding the set weight is also controlled. All the data is displayed by the SCADA system available only in the factory LAN.
The implementation is characterized by a high level of security, meeting stringent requirements to ensure the safety of operators and maintenance staff. For example, three high-speed doors, each fully compliant with the requirements of harmonized standards for movable guards approved for human contact. The safety curtains that enclose the buffer zone are made with the highest resolution available on the market.
Access to the service area is provided by a wicket in the system partition equipped with a combination of redundant security features: safety anti-lock handle, a reset switch for the local part of the safety circuit and a security device for a LOTO padlock. The access platform to the machinery room of the vertical conveyor is secured around the perimeter with a full guardrail and curbs. Access from the ladder basket is via a self-closing frame gate. The drive unit was enclosed in a removable enclosure.
Aware of the risk posed by transport between two separate fire zones, we paid special attention to the construction of the fire gate and its integration with the conveyor control system. The selected algorithm minimizes the risk of blocking the transported unit in the clearance of the fire gate.
Limited space was an important design challenge. The stand on the first floor was located in a narrow transport corridor. With a large measure of confidence, the new building was adapted for the installation of a symmetrical transport system, adjacent to the presented implementation. Further expansion plans make it possible to use the existing loading bays or to solve an independent system with new workstations.
The 2020 implementation coincided with the first months of the global pandemic state, including numerous difficulties in international logistics and restrictive health restrictions for subcontractor employees. The implementation is a valuable experience for us, confirming the rightness of our flexible approach to changing environmental conditions and customer requirements.
« powrót